Lubrication and Lubricants
A key prerequisite for the low-wear (or even wear-free) operation of a ball screw is the reliable separation of the surfaces of the rolling elements and the ball raceways with a suitable lubricant. An
- oil lubrication or
- grease lubrication
is used to achieve increased wear protection in the ball contact points and to effectively prevent any surface damage in the event of an overload.
Lubricating film thicknesses of just a few tenths of a micrometer between the friction partners is sufficient for reducing the contact of the rolling and sliding surfaces. In addition, the lubricant very effectively protects the ball screw from corrosion. Depending on the type of lubrication (e.g. oil circulation lubrication), the frictional heat generated in the contact points is also dissipated, wear particles as well as impurities are flushed out of the nut and the sealing effect of the wiper systems is also supported (e.g. through a grease collar).
The lubricant should ideally sufficiently wet all of the functional surfaces present in the ball screw at all times and in all frictional states. These surfaces can also be found in the ball returns in addition to the ball raceways.
Permissible and Impermissible Lubricants
In general, most commercially available mineral oils and mineral greases are suitable for lubricating ball screws. In order to effectively increase the wear service life, we recommend using suitable lubricants, preferably in combination with program-controlled central lubrication systems. Synthetic oils and greases in particular have proven effective for applications with high travel speeds. Synthetic lubricants are also made from crude oil. However, they contain more highly-refined base oils than conventional mineral oil lubricants. The impurities present in crude oil are largely removed and the individual oil molecules are tailored to the desired lubrication requirements. Synthetic lubricants thus receive a higher level of purity and quality, which makes it possible to achieve an improved lubricating effect. They also usually have a much better flow capability and a higher temperature stability.
Solid lubricating additives, such as graphite, molybdenum disulfide, etc. (as dry lubrication or dispersed in oil) are not permissible, since they only apply a very thin layer on the functional surfaces and only remain functional for a long time at very moderate speeds and low pressures. No conventional lubricants may be used in special ambient conditions, such as continuous vibrations, application in clean rooms, a vacuum and under particularly high or low temperatures. Special lubricants should be used in these application cases.
Lubrication and Frictional States
The frictional and wear behavior and the achievable service life of the ball screw depend on the lubrication and the resulting frictional state. The possible lubrication states are delimited in the Stribeck curve, which shows the dependence of friction (µ) on the sliding speed (v). At rest (v = 0), the static friction is present with very high frictional values. The static friction is also responsible for the breakaway torque when the ball screw starts moving. With increasing sliding or travel speed, different lubrication states form (boundary, partial and full lubrication).

Stribeck Curve of the Lubrication States
Only partial fluid friction exists with the boundary lubrication (1). The existing lubricating film thickness is insignificantly small and there is predominantly solid body contact. An insufficient lubricant quantity, an insufficient operational viscosity or relative movement of the frictional partner lead to this state. If the lubricant contains suitable additives, then there are reactions between the additives and the metallic surfaces in the event of high pressures and temperatures at the contact points. Lubricating reaction products form, which can create a thin boundary layer (in the nanometer range). This can lead to the complete separation of the surfaces and is comparable in its effect to a full lubrication.
The so-called mixed friction exists with the partial lubrication (2). As with the boundary lubrication, there is partial solid body contact of the surfaces. However, the lubricating film thickness is still too small for a full lubrication.
With the full lubrication (3), the surfaces that move relatively to each other are completely or almost completely separated by a lubricating film. There is almost a purely liquid friction without solid body contact.
In highly dynamic machine tools in particular, ball screws carry out an extreme number of start and stop processes that are associated with high acceleration and significant inertial effects of large masses. In the process, the rolling partners in the ball screws (i.e. balls, nuts and spindles) are often in the transition area between partial and full lubrication. This transition area is also called the mixed friction range. However, the ideal lubricating state of full lubrication is usually achieved for ball screws only at rapid speeds.
All three states occur for oil and grease lubrication. The oil lubricating state for grease lubrication is primarily determined by the viscosity of the base oil. In addition, the thickener in the grease acts to form a lubricating film.
Load Magnitudes for Ball Screws
Ball screws are heavy-duty drive elements whose load is usually more than 15% of the dynamic load rating due to the axial force (Fa > 0.15 Cam). Hertzian pressures of 2,000 to 4,000 MPa (N/mm2) are produced here at the ball point of contact. The travel speed and therefore the speed of the ball screw is rather low compared to spindle bearings and is usually less than 4,000 rpm. Precise knowledge of the load magnitudes acting on the ball screw is absolutely required to design an optimal lubrication.
A minimum load is required to ensure the rolling process of the rolling elements. It is usually realized with the preload force for preloaded ball screws. The ratio C0/F < 60 serves as a reference value.
Hydrodynamic Lubrication
In the event of hydrodynamic lubrication, the lubricant is conveyed into the narrowing lubrication gap through the relative movement of the contact surfaces. In the process, an extremely high pressure is generated in the immediate contact zone, which briefly leads to an increased lubricant viscosity and allows for the separation of the contact surfaces.
Since the viscosity increases with an increasing load and the contact surfaces increase due to elastic deformation, the effect of the load is rather low. However, the rolling speed, the dynamic viscosity and the pressure-viscosity coefficient do have a major effect on the minimal lubricating film thickness.
Elastohydrodynamic Lubrication
The elastic deformation of the contact bodies and the hydrodynamic influences are combined in the theory of elastohydrodynamics (EHD). The EHD theory is specifically used for the lubricating state in the roller contact and provides the basis for calculating the lubrication effect on damage. That is also why the service life calculation of ball screws pursuant to DIN ISO 3408 requires an elastohydrodynamic (EHD) lubricating film between the rolling partners.
Loss of Lubricant
In principle, there is no hermetic seal between the nut and spindle (such as with a shaft sealing ring) due to the geometric relationships of the screw of a ball screw. There is always a small discharge of lubricant, even in optimally designed wipers. That is why there is always a loss of lubricant that must be compensated for across travel paths or over time.
Lubrication Cycles
The re-lubrication intervals and the lubricant quantities depend on the operating data, the application conditions and the ambient conditions. They must always be determined and specified with respect to the application case. The specifications of the lubrication cycles are therefore only recommendations, which always require an empirical confirmation or correction.
Viscosity
The lubricating oil, for example, must have a certain viscosity to form a stable lubricating film in the contact areas between the rolling elements and ball raceways. There are technical functional limits for the oil viscosity. These limits result from:
- increasing mechanical power losses, especially at higher idling friction,
- higher operating temperatures and
- poor conveyance capability of highly viscous oils.
The viscosity of a lubricating oil reduces with an increasing temperature. That is why it is important that the required viscosity exists, especially at operating temperature. However, the viscosity also changes with increasing pressure. The pressures in rolling contact calculated according to Hertz are up to 4,000 MPa under high load and lead to an increase in viscosity.
Highly-viscous lubricants have the advantage that they minimize the metallic contact of the rolling partners during dynamic starting and stopping processes and reduce the mixed friction proportion and therefore adhesion and abrasion (i.e. friction and wear of the rolling partners). If predominantly higher spindle speeds are realized, however, an expected higher heat deviation is disadvantageous.
Low viscosity oils have a lower heat deviation. That is why the mixed friction range occurs earlier under load. They spread more easily and support the flushing out of dirt particles that have collected in the nut. Larger lubricant quantities are therefore required than with highly viscous oils to be able to achieve a sufficient and above all safe lubrication. Compensation via the lubricant quantity, however, is only possible to a limited extent with two to three viscosity classes.
Oil Lubrication of Ball Screws
The achievable service life values of oil-lubricated ball screws are superior to those with grease lubrication in principle, provided an elastohydrodynamic (EHD) lubrication can be achieved for a significant part of the work cycle.
In order to achieve an increased wear protection in the mixed friction area in the ball contact points and to effectively prevent any surface damage (such as seizure marks) in the event of an overload, it is required and recommended to use CLP lubricating oils with EP additives (wear-reducing additive) according to DIN 51517 part 3.
If the wear-reducing additive is missing, the lubricating oil will be pressed out of the lubricating gap in the event of a high Hertzian pressure (2,000 to 4,000 N/mm2 is characteristic for ball screws) and no stable lubricating film can form, even at low speeds. This inevitably leads to a higher wear rate and a reduction in service life.
CLP lubricating oils are also characterized by a good aging resistance. In addition, highly-viscous lubricating oils improve the running quality and reduce the noise development of the ball screw.
Lubricating Oil Viscosity
The lubricating oil viscosity is also very important. Highly loaded ball screws require highly viscous lubricating oils so that the elastohydrodynamic lubricating film can form between the rolling partners.
This lubricating film must not only be present at ambient temperature (up to 40 °C), but also must be reliably present at higher operating temperatures (up to about 80 °C), even though the oil viscosity is significantly lower due to the temperature. At a temperature increase of 40 °C to 50 °C, a ISO VG 220 oil loses two viscosity classes.
Lubricating Oil Recommendation
That is why we recommend using the lubricating oil CLP 220 (DIN 51517) for highly-loaded precision ball screws. It is also generally possible to use the lubricating oil CLP 150, whereby the lubricant dosage should be increased by about 30%. In order to ensure a reliable lubrication, low-viscosity lubricating oils (also due to the lower pressure stability) should not be used if possible, since the lower oil viscosity also cannot be compensated for, even with significantly more lubricating oil.
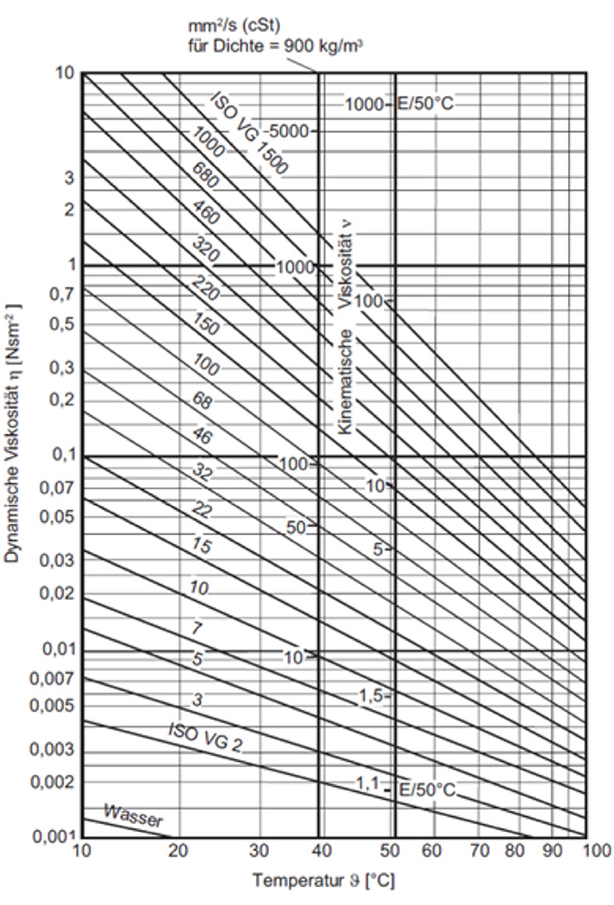
Dynamic viscosity of lubrication oils on a mineral oil basis depending on the temperature
Lubricating Oil Quantity
The required lubricating oil quantity depends on the spindle data (nominal diameter, pitch, ball size, number of loaded turns and design) and the operating data (load, speed and installation position). Since the ball screw nuts are usually equipped with wiper systems that also make lubricating oil discharge difficult, the nuts may overheat if over-lubricated and at high speeds. In order to achieve a good lubricant distribution, a frequent lubricating oil supply in small quantities is more favorable than an infrequent supply in large amounts. The lubricating oil injection intervals should occur about 3 to 4 times per hour.
Oil Filtration
The purity and the temperature of the lubricating oil are important. A sufficiently effective oil filtration (mesh size < 10 µm) is advisable so that neither impurities nor solids enter the ball screw with the lubricating oil. This increases the ball screw service life and the reliability of the lubrication.
Oil Cooling
In addition to the lubrication, the lubricating oil also has the task of cooling the ball screw or at least quickly dissipating the resulting frictional heat. That is why the lubricating oil should be kept at a sufficiently low operating temperature by an oil cooler. The cooling temperature of the oil cooler (oil inlet temperature about 40 °C) should not be chosen to be too low in order to avoid an undesired formation of condensate. The oil temperature of 40 °C also makes it easier to assess the lubricating oil, since the base oil viscosity is specified at this temperature for most oils.
CPL 100 for Preservation
If no special lubricating specifications are required by the operator, the functional check and the delivery of the ball screw occurs with the lubricating oil CLP 100 (DIN 51517-3). The lubricating oil wetting upon delivery is exclusively for preservation purposes and does not replace any service lubrication. The highly-viscous lubricating oil flushes out the preservative oil already after a short time or mixes with it so that no cleaning is necessary before commissioning the ball screw.
Track and Hydraulic Oils
According to the specifications of various oil manufacturers, track oils (e.g. Mobil Vactra, BP Maccurat or Aral Deganit) can also be used for lubricating linear guides, gearboxes, bearings and ball screws in machine tools. Since most track oils lack the necessary pressure additives, we do not recommend using track oils as a lubricating oil for ball screws, even if they are suitable for "high pressure!" The same applies to hydraulic and hydrostatic oils!
Oil Mist Lubrication
An oil mist lubrication on the spindle shaft is only recommended for nut designs without a wiper (prerequisite: no or only very little contamination). An oil mist lubrication as a minimum quantity injection lubrication of the ball screw nut is only permissible and possible with a nut specially designed for this type of lubrication. Oil bath or oil splash lubrication should only be used at low travel speeds. Drip oil or loss lubrication is possible in principle, but the necessary lubricating oil quantities must be observed.
Grease Lubrication of Ball Screws
The principles of EHD theory generally also apply to grease lubrication. Grease offers good protection against corrosion and the penetration of impurities. Grease lubrication is relatively simple and low cost compared to oil lubrication.
Lubricating Greases
A grease is to be chosen while taking the load and the speed into account according to the NLGI class as defined in DIN 51878. The following lubricating greases were tested in use with AM ball screws and are approved by us!
Item | Manufacturer | Designation | NLGI class | Base oil viscosity mm2/s at 40° |
---|---|---|---|---|
1 | Shell | Shell-Alvania EP2 | 2 | 186 |
2 | Optimol Industrie GmbH | Optimol Longtime PD2 | 2 | 94.9 |
3 | Lubricant Consult GmbH | Turmogrease P 1002 BDY | 2 | 110 |
4 | Exxon Mobil | Mobilith SHC 100 | 2 | 100 |
5 | Klüber | Klüberplex BEM 34-132 | 2 | 130 |
6 | - | - | - | - |
7 | Interflon | Fin Grease MP 00 | 00 | 105 |
8 | Klüber | Klübersynth G 46-1200 | 00 | 120 |
9 | Castrol/Tribol | Tribol 3020/1000 | 00 | 186 |
10 | - | - | - | - |
Grease Service Life
The grease service life is the time in which the tribological functionality of the ball screw is maintained without new grease being added or losing existing grease. This characteristic value of the lubricating grease describes the aging of the grease and, among other things, depends greatly on the type of lubricating grease. With the greases normally used to lubricate ball screws, the service life is between 5,000 and 20,000 hours of operation, which is thus often shorter than the fatigue life resulting from the load duty cycle and the dynamic load capacity of the ball screw.
The grease service life is not as important for ball screws as is the case for life-long lubricated rotary bearings, for example. This is due to the unavoidable loss of the grease fill quantity due to the continuous axial stroke of the nut. At the same time that the lubricant is transported to one side of the nut, impurities and pollutants adhering on the other side are transported into the nut. That is why the use of wipers at the ends of the nuts is absolutely necessary, especially when using grease lubrication, since these make both transport effects difficult. Nevertheless, new grease must be added cyclically to compensate for the lost amount and due to the grease contamination.
Initial Filling
The nut of the ball screw is normally not filled with grease in the delivered state, but rather is provided with a preservative oil. Since the preservative oil is compatible and mixable with the lubricating greases we recommend, this does not have to be removed before the initial grease filling.
The initial filling with lubricating grease then usually is done by the user and should not exceed 50% of the free nut volume, as otherwise (especially at high speeds) there is a risk of overheating and thus damage. The required amount of grease depends on the size and design (individual or double nut) of the ball screw. So that the grease can distribute better in the nut, it should be filled in three partial amounts with a time delay. Between the partial fillings, the ball screw should be moved at low speed.
Re-Lubrication Intervals
The re-lubrication intervals are usually to be determined individually in practice, since they are dictated by influencing factors such as load, speed, temperature, ambient influences, installation position and pollutants, among other things. Under normal operating conditions, however, re-lubrication cycles of 200 to 300 hours (corresponding to a mileage of about 150 km) are quite sufficient. In practice, the re-lubrication intervals (per hour) are realized with very small amounts of grease (e.g. 0.1 cm3) in significantly shorter time periods.
If no detailed operating conditions are known, the re-lubrication amount for double nuts can also be approximately determined as 0.010 cm3 (at high load) or 0.003 cm3 (at normal load) per 10 mm spindle diameter. This re-lubrication amount may only serve as a reference value and may deviate significantly from the actual required amount.

Ball screw with scraper for grease lubrication
a ≤ 0.15 Cam) without EP additives | Lithium soap greases (Fa > 0.15 Cam) with EP additives | Synthetic special greases | |||
---|---|---|---|---|---|
0 | 355-385 (semi-liquid, liquid grease) | - | heavily loaded up to 800 rpm | High-speed application up to 4,000 rpm | |
1 | 310-340 (very soft) | low load up to 800 rpm | - | High-speed application up to 4,000 rpm | |
2 | 265-295 (soft) | normal load up to 600 rpm | very heavy load up to 600 rpm | High-speed application up to 4,000 rpm | |
3 | 220-250 (medium-strength) | heavily loaded up to 400 rpm | - | - |
Direct to our service
Your request to us
Use our professional competence to develop the best solution. Our engineers can be reached directly under
+49 2191 989-200